What are the different types of woodscrews, and which one is best?
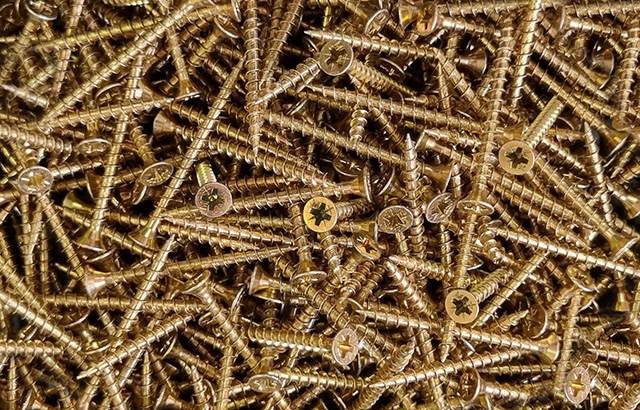
A woodscrew is one of the most versatile fastenings found within the construction industry and there are multiple different types of woodscrews. They can be used to screw timber together, attach hinges and ironmongery to windows, doors, and cabinets, mount fixtures to walls with the aid of a plastic plug, and fix window and door frames in place.
Used by joiners, builders, electricians, and plumbers alike – the simple woodscrew is a critical component in many construction projects.
In this article we are going to discuss:
- What is a woodscrew?
- What are the different types of woodscrew?
- MX woodscrew manufacturing process – woodscrew wire, woodscrew head and thread, woodscrew heat treatment and plating, woodscrew lubricant and woodscrew boxes.
- Woodscrew comparison video.
- Best wood screw summary.
What is a woodscrew?
Using a spiraling thread around a cylindrical core was first used to make practical devices such as olive and grape presses. It is believed these tools were being used around the first century and were made from wood.
A woodscrew uses the same concept but instead, wraps a thread around a steel shank that has a head on it, which is used to drive the fastener. Every turn of the head advances the thread into the base material.
The head of the woodscrew not only allows the fastener to be turned, but it also pulls materials together and holds fittings in place – such as when mounting a hinge on a door.
What are the different types of woodscrew?
Countersunk woodscrews are by far the most popular type and they are what we will be focussing on in this article.
Woodscrews have evolved over the years; progressing from slotted heads and tapered shanks to Pozidrive twin-threads, single-threaded, metric-sized, multi-purpose screws.
More recently, we have seen several new types of wood screws enter the market with features that are designed to offer the end user benefits such as; easier countersinking, reduced splitting, and the elimination of pilot drilling. There is no doubt that some of these concepts work and do indeed support the design, but when considering our own MX woodscrew we observed some drawbacks as below:
- Countersinking ribs – ribs or fins which protrude from the underside of the head are designed to chop away at the timber, countersinking the surface. Whilst effective they destroy surface plating on hinge recesses and bracketry which is unsightly and can cause premature corrosion.
- A reduction in splitting can be achieved by machining grooves into the shank of the woodscrew or adding knurling to the core of the screw. Grooves allow the displaced material somewhere to expand into, and knurling simply enlarges the hole, making it easier for the shank to pass through. Both features do work, but on compacted boards such as MDF, splitting is still likely to occur. The other downside of these designs is when this type of screw is used inside a plastic plug. The sides of the plug need to be pushed apart by the core of the screw so that it expands in the hole. Slashes or grooves reduce the expansion of the plug and knurling reams out the insides, each compromising the fixing’s performance in masonry or brick.
- Although Maxitek MX woodscrews are manufactured for extremely demanding tasks and will not snap, even when driven into hardwoods or dense boards without pilot drilling, we simply regard this as bad practice. We have also seen also serrated and arrow-shaped tips feature on woodscrews, which is supposed to negate pilot drilling. In reality, none of these designs remove enough of the timber to clear a path for the core of the screw. A simple pilot hole is the only sure way to avoid stressing the wood or board. This eliminates splitting and bulging, it also ensures the full circumference of every thread is engaged in the base material.
Top Tip
The Trend UNI/CS countersink is fully adjustable and combines a pilot drill and countersink function in one handy accessory.
“Having explored and committed numerous designs into working trials we decided that our Maxitek MX woodscrew should serve as a premium quality, multi-purpose screw for all joinery and construction trades.” Craig Sanders, Joint Managing Director at Protrade.”
MX Woodscrew Manufacturing Process
At a glance, most woodscrews look the same. It is not until you understand the entire manufacturing process that you appreciate how much time and effort goes into making this essential but often underappreciated fastener. We explain the entire process below:
Woodscrew Wire
Selecting the right raw material is critical.
Every delivery of wire to manufacture a Maxitek MX wood screw is accompanied by a certificate of conformity that shows the chemical material composition and physical features – such as yield and tensile strength.
Further in-house testing is also performed using specialist equipment:
- Laser spectrometer – Chemical composition inspection.
- Metallographic microscope – Annealing testing.
- Tensometer – Tensile and yield evaluation.
As the MX range extends from 3.0mm to 6.0mm, only 5.5mm and 6.0mm diameter wire is sourced. The 5.5mm is used for all sizes up to 5.0mm and unsurprisingly, 6.0mm is used for 6.0mm screws. The process of drawing the wire involves phosphating, drawing, and annealing – multiple times.
- The phosphate coating acts as a lubricant when the wire is drawn through the machine and also provides corrosion protection.
- Drawing stretches the wire to the correct gauge.
- Annealing conditions the wire, making it more ductile for drawing, threading, and punching.
Woodscrew Head
Once the wire has been drawn to the correct size it is now ready to be made into a woodscrew.
Heads are cold-formed using a punch-and-die process. Dies form the shape of the head, whereas a punch creates the drive recess.
Head and thread design dramatically affects how a woodscrew will perform in use. You can see from the drawing below that there is a great deal of detail to consider:
The Pozidrive recess has been widely adopted by many fastener companies and is popular with tradespeople. On initial inspection, all Pozidrive screws look the same but there are hundreds of variations due to the individual geometry of each brand and the open market dies that are available for the less discerning ‘own brand’ fastener buyer.
Maxitek MX woodscrews have a countersunk Pozi head that is unique and has been engineered with meticulous attention to detail. Each screw is stamped with the MX logo for easy identification – the only reference to the certified product once it’s been inserted.
- To prevent the head from rounding out, the screwdriver bit must engage with the screw securely. This is achieved using a unique punch that creates a wide and deep recess so the bit can penetrate the head of the screw.
- The shape of the double countersink (ref X/Y) is designed to make sure that enough material remains around the Pozi recess after punching. This eliminates weakness and resists deformation and snapping.
- Although the recess must have a snug fit around the screwdriver tip, it must allow the bit to release, thus avoiding the bit from becoming stuck in the screw.
- The thickness of the round edge (ref U) is kept to a minimum, so the screw sits flush when inserted into hinges and countersunk ironmongery.
Woodscrew Thread
The angle of the thread and the number of threads per inch (TPI) decide on the screw’s insertion speed and its holding power. There is an important balance between the two and unlike other woodscrews which share the same TPI across the entire range, MX screws use a higher thread pitch on screws up to 25mm to improve holding power, and a lower TPI on longer screws to make installation faster. Effectively, each thread is an anchor point in the substrate, so short screws with a higher thread count will have improved pull-out compared to a screw with very few threads.
The picture below illustrates two screws of the same size with a different thread pitch – the MX on the left gives a much stronger hold with twice the number of anchor points.
Another consideration is whether to offer a partially threaded or fully threaded design?
Once the thread is cut in both materials a fully threaded screw will hold the materials in place, whereas a partially threaded screw uses the smooth part of the shank and the underside of the head to pull the materials together – giving a very tight joint.
MX woodscrews are fully threaded up to 55mm in length and partially threaded thereafter. We believe this allows us the best combination of holding power on board materials and the tightest joints possible on thicker natural timbers.
Finally, where the thread starts at the tip of the screw is important. A sharp point will pierce the surface of the material, but it will not pull the screw forward. The thread on a Maxitek MX woodscrew starts at the very end of the tip so it engages with the substrate almost instantly, drawing the screw in.
Woodscrew Heat Treatment
Carbon steel woodscrews are heat treated to give them the strength required for insertion and load bearing. The screws are heated in huge industrial ovens before being cooled in oil to meet the desired hardness. The oil used in this process is continually recycled to reduce any environmental impact.
A woodscrew that is very hard may well resist the Pozi drive becoming deformed should the screwdriver bit slip, but it will leave the screw brittle and therefore likely to snap upon insertion into harder materials. A screw that is too soft will shear easily and suffer from cam out when being turned, it is also prone to bending under load.
The heat treatment process MX woodscrews go through means they can be used in soft and hardwoods as well as dense board materials, without the risk of snapping. High pull-out values and loadings are also achieved.
Woodscrew Plating
Once the forming and heat treatment of the screw has taken place, the raw steel needs to be plated so it is protected from corrosion and has an attractive appearance. MX screws have a fine layer of zinc plating applied in both bright zinc and yellow passivated finishes, meeting service class levels 1 and 2 according to EN 1995-1-1, part of the criteria for achieving their UKCA and CE approval.
Offering an extensive range of sizes in bright zinc-plated BZP and yellow zinc-passivated YZP, allows customers to match the colour of the screw with that of the hinge or fitting. After all, a yellow woodscrew mounted to a zinc kitchen cabinet hinge is an undesirable focal point and detracts from the quality and overall appearance of the furniture.
The adherence of the plating to the bare metal is critical. If the layer of zinc is poorly attached, corrosion protection is severely compromised and rust will appear. Another issue with sub-standard plating arises at the point of insertion – when they are being held between the thumb and forefinger. Screws that have not been plated correctly cause flakes of the coating to come away and get stuck in the fingers of the operator. It doesn’t sound like a big problem, but these tiny cuts can become infected and if nothing else, it’s uncomfortable.
The plating process for Maxitek screws adheres to strict government regulations concerning air and water pollution in a compliant and certified facility.
Woodscrew Lubricant
The application of a lubricant is designed to make the insertion easier, although it is not adopted by every manufacturer as it adds to the cost. I am sure that most of you reading this article will have heard a screw squealing as it’s driven into MDF before; this is due to a lack of lubricant, or a poor-quality coating having been applied.
The lubricant on a Maxitek MX woodscrew has been shown to reduce installation torque by up to 50%.
A short comparison video of a Maxitek MX woodscrew versus a competitor wood screw can be seen here:
Using a premium lubricant on Maxitek MX woodscrews has the following benefits:
- Much easier to drive in by hand or cordless screwdriver.
- Prevents screwdriver bits from slipping, thus reducing bit wear.
- More screws can be inserted per battery charge, when using cordless tools.
- Easier driving when inserting screws in confined spaces.
- Much less likely to snap.
Woodscrew Boxes & Packaging
Often overlooked, the box that the screws come in, is very important. We have incorporated these features into the packaging of our Maxitek MX wood screws:
- The box is designed to be strong, rigid, and retain its shape. Nobody wants to receive a delivery to find that the boxes inside have collapsed and all of the sizes are mixed up. For users with stores, the boxes must be able to be stacked on top of one another and remain upright.
- Large and easy-to-read labels. MX woodscrews feature a bright yellow label for yellow screws and a white label for zinc screws so the user is instantly aware of the plating colour.
- Other information present on the label:
- Metric and imperial sizing.
- Bit size required.
- Number of screws in the box.
- Large barcode to accommodate barcode-picking systems.
- We have chosen a wraparound label so the information can be read on the top and end of the box. This enables easy identification from above and side on, for example, if placed on the floor or when browsing from shelves in a storeroom.
- Large internal side tabs for resealing the box once opened, thus reducing waste.
- Outer carton batch identification for traceability.
Summary
The humble woodscrew is such a common product on the job site, it is often taken for granted. They can be used in lots of critical applications, work in many materials, hold very heavy loads, and remain in place for years – if not decades.
“In virtually every joinery application the three key components are wood, glue, and screws – don’t compromise on any one”– Craig Sanders, Joint Managing Director at Protrade.
Despite all of this, they are often under-researched and purchased as a low-cost consumable rather than an integral part of the build – be that a piece of furniture or a refurbishment project.
We hope that this insight into the manufacturing process of Maxitek woodscrews encourages users to consider trying a well-engineered product on their next project and benefit from our desire to create a fastener that is dependable and consistent, like comparable professional screw brands – including Reisser, Spax, and Heco.
For more information on the MX professional woodscrew range, please click below.
Explore our range of Maxitek MX Woodscrews
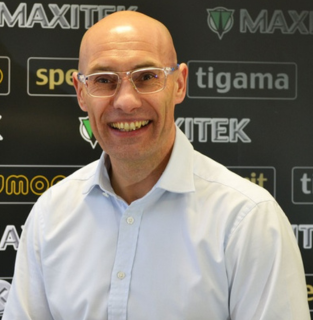
Joint Managing Director, Protrade
Des has over 30 years of experience at Protrade, having worked in the capacity of Sales Co-ordinator, Account Manager, and product development, culminating in being appointed Joint Managing Director in 2018.